So schön die Kombi aus Fels und Meer ist: Sie birgt auch Gefahren. Denn die salzig-feuchte Luft lässt Bohrhaken schnell korrodieren. Dies ganz besonders, wenn beim Einbohren nicht das richtige Material verwendet wurde.
Das Risiko bei Bohrhaken am Meer
Im Oktober 2014 hatten drei Kletterer am Monte Monaco auf Sizilien beim Abseilen den Schreck ihres Lebens: Während am Stand – zwei Bohrhaken mit einer Schlinge verbunden – zwei von ihnen gesichert waren und der dritte gerade von diesem Stand abseilte, brach der beim Abseilen belastete Bohrhaken. Zum Glück hielten die Schlinge und der zweite Bohrhaken, sonst hätte dieser Hakenbruch wohl fatal geendet. Der Beinahe-Unfall sorgte damals für einiges Aufsehen. Zumal zuvor bereits ähnliche Hakenbrüche unter geringer Belastung aus den tropischen Klettergebieten in Thailand bekannt geworden waren. In Fachkreisen kam eine Diskussion um die Sicherheit von Bohrhaken in Meeresnähe auf. Auch aus Sardinien sind mittlerweile ernste Unfälle aufgrund von Hakenversagen bekannt. Zwar sind Hakenbrüche im maritimen Umfeld bisher nicht alltäglich. Doch die Korrosion in Meeresnähe ist ein Problem, das in den nächsten Jahren noch zunehmen könnte, wie Gerhard Schaar als Spezialist fürs Einrichten von Routen erklärt: "Die großen Erschließungswellen vieler bekannter, meernaher Klettergebiete liefen in den 90er- und 2000er-Jahren. Diese Haken kommen jetzt so langsam an ihr Lebensende."
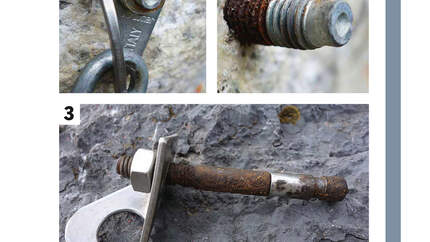
Korrosion bei Bohrhaken
Bekanntlich ist nichts für die Ewigkeit, und das gilt auch für Bohrhaken im Fels. Wobei gut gesetzte Klebehaken oder einzementierte Haken sehr lange Zeiträume hohe Sicherheit bieten. Es gibt 50 Jahre alte Bühlerhaken im fränkischen Fels, die immer noch einwandfrei sind. Doch Sizilien, Sardinien oder Kalymnos sind nicht das Frankenjura. Jeder Stahl oxidiert irgendwann, wobei dieses "irgendwann" von der Korrosionsbeständigkeit des Stahls und den Umgebungsbedingungen abhängt: Je wärmer, feuchter und salzhaltiger die Umgebung ist, desto stärker werden Bohrhaken angegriffen. Dazu kommt die Chemie des Gesteins: Im Kalk rosten Haken wegen des Kalzium- und Magnesiumanteils schneller als im Granit. Und offenbar geschieht dies in rotgelben, oft versinterten Kalküberhängen schneller als in grauen Platten.
Dass Haken rosten, ist nicht Neues. Alte Schlaghaken in den Alpen bezeichnet man, wenn sie eine Weile im Fels steckten, aus gutem Grund als "Rostgurken". Solche Schlaghaken bestehen aber aus normalem Stahl. Bei Bohrhaken kommen dagegen unterschiedliche Stahlvarianten mit unterschiedlicher Korrosionsbeständigkeit zum Einsatz. Einen Überblick gibt die Tabelle unten. Verzinkter Stahl hat sich als Bohrhakenmaterial als nur sehr wenig korrosionsbeständig erwiesen und sollte überhaupt nicht mehr als dauerhafte Absicherung angebracht werden. Einziger Vorteil: Die verzinkten Haken neigen dazu, flächig eine Rostschicht auszubilden, was sie schon rein optisch als unzuverlässig kennzeichnet.
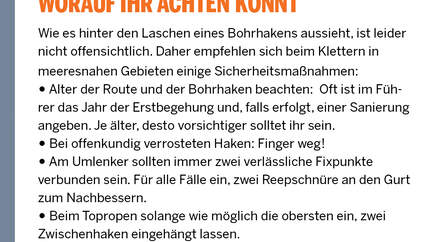
Bohrhaken aus Edelstahl
Bei Edelstahl funktioniert die Korrosion etwas anders. Edelstählen ist neben dem Grundmaterial Eisen auch Chrom (und, je nach Art und Güte, Nickel, Molybdän oder Kupfer) beigemischt. Durch die sogenannte Passivierung bildet sich auf der Oberfläche des Stahls eine Chromoxidschicht aus, die vor weiterer Oxidation schützt. Wird diese Schutzschicht beschädigt – durch Kerben (beim Einschlagen des Bohrdübels mit dem Hammer), durch Spannungsrisse beim Anziehen des Bohrhakens, durch Schweißnähte –, kann sich von diesen Schwachstellen aus die Oxidation ins Innere des Materials fressen. Das Problem dabei: Auf den ersten Blick ist so ein Schaden kaum zu erkennen, schon gar nicht, wenn er den Bohrhakendübel hinter der Lasche betrifft. Die Spannungsrisskorrosion ist nach Untersuchungen der UIAA wohl auch das größte Problem bei Bohrhaken in Meeresnähe.
Es gibt schließlich noch eine dritte Variante der Korrosion, die galvanische Korrosion. Die tritt auf, wenn Stähle unterschiedlicher Güte miteinander verbaut werden, also zum Beispiel der Dübel aus verzinktem Stahl, die Lasche aber aus Edelstahl besteht. Am korrosionsbeständigsten ist aber nicht Stahl, sondern ein anderes Metall: Titan. Bohrhaken aus Titan lassen sich nur als Klebehaken herstellen, die dann eine sehr lange Lebensdauer aufweisen.
Eine Frage des Preises
Generell gilt heute hochwertiger A4-Stahl (AISI 316 und 316L) als Goldstandard für normale Klettergebiete. Dieser Stahl ist sehr korrosionsbeständig. Laut Maurizio Oviglia aus Sardinien, der sich dort viel um das Einrichten und Sanieren von Routen kümmert, sind ihm noch keine Hakenbrüche mit A4-Stahl bekannt. Oviglia fordert deshalb auch, dass dieser Stahl die Mindestqualität in Meeresnähe sein müsse. Wobei auch A4-Stähle nicht dauerhaft für unmittelbare Meeresnähe geeignet sind. Deutlich besser als A4-Stahl ist sogenannter HCR-Stahl, den bisher nur die Hersteller Climbing Technology und Petzl im Programm haben. Wie gesagt sind Titan-Haken in hochkorrosiven Umgebungen das Nonplusultra. Warum werden also nicht alle Routen in Meeresnähe mit dem besten Material eingerichtet oder saniert? Das ist, abgesehen vom Arbeitsaufwand, in erster Linie eine Preisfrage: Ein A4-Petzl-Bohrhaken kommt komplett auf rund 7,50 Euro, ein HCR-Bohrhaken von Climbing Technology oder Petzl dagegen auf rund 30 Euro. Eine Route mit 10 Bohrhaken und einem Umlenker auszustatten, kostet mit HCR-Stahl also über 300 Euro.
Titanhaken sind etwas günstiger als HCR-Stahl, müssen aber geklebt werden, was die schnelle Verarbeitung – besonders bei flächendeckenden Sanierungen oft erwünscht – erschwert. Wobei Gerhard Schaar von bolting.eu darauf hinweist: "Das wird irgendwann auch zu einer kletterethischen oder optischen Frage: Wollen wir an den Felsen irgendwann vier Generationen von Bohrhaken nebeneinander stecken haben? Und ist es nicht auch finanziell günstiger, einmal richtig zu sanieren als immer wieder damit anzufangen?"
Augen auf am Fels
Beim Klettern in Meeresnähe heißt es: Augen auf! So sicher die Mehrzahl der Bohrhaken sein mag und so selten Hakenbrüche bisher sind: Ein Blick auf den Zustand der Absicherung ist immer zu empfehlen. Bei sichtbar oxidierten Bohrhaken gilt auf jeden Fall äußerste Vorsicht. Erschließer und Sanierer sollten möglichst das beste Material für die jeweilige Umgebung verwenden. Wer nicht sicher ist, findet unter bolting.eu Workshops und Kurse oder wendet sich an die alpinen Verbände. Wobei letztere neben den lokalen Tourismusbehörden eventuell auch bei den Materialkosten unterstützen können. Im Frankenjura kümmert sich die IG Klettern um Sanierungen und Haken.
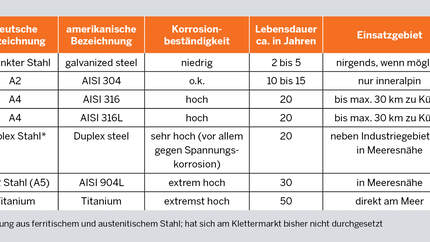
Die als Bohrhaken verwendeten Stähle sind durchweg Legierungen von Eisen und anderen Metallen, daneben können sie geringe Anteile an Kohlenstoff oder Schwefel enthalten. Alle Stähle enthalten Chrom, die Stähle der A-Klasse (wie A2, A4, A5 oder HCR = high corrosion resistant) sind austenitische Stähle, bei denen die Zugabe von Nickel zu einer höheren Korrosionsbeständigkeit gegenüber reinem Chromstahl führt. Die A4-Stähle enthalten zusätzlich Molybdän, A5- oder HCR-Stahl zusätzlich noch Kupfer. Ganz generell gesprochen nimmt mit höheren Anteilen von Nickel, Molybdän und Kupfer die Korrosionsbeständigkeit zu, ebenso aber der Preis des Stahls. HCR-Stähle sind extrem beständig, besonders gegen Spannungsrisskorrosion. Kein Stahl, sondern ein eigenes Metall ist Titan. Titan gehört zu den Leichtmetallen, im früheren Ostblock waren Eisschrauben und Haken aus Titan weit verbreitet (und superleicht). Es bildet an der Luft eine äußerst beständige oxidische Schutzschicht (Passivierungsschicht), die es selbst gegen Meerwasser-Einfluss schützt. Titan ist nur mäßig hart, Titanlegierungen haben aber eine hohe Zugfestigkeit. Titanbohrhaken lassen sich nur als Klebehaken herstellen. Generell sind Klebehaken als korrosionsbeständiger anzusehen. Sie werden spannungsfrei eingesetzt, so dass Spannungsrisskorrosion kaum ein Problem darstellt. Zudem ist das Bohrloch durch den Kleber vor eindringender Feuchtigkeit geschützt. Wichtig ist allerdings, bei Bohrhaken in Meeresnähe einen Kleber zu verwenden, der vom Hersteller für solche Umgebungen zugelassen ist. Beim Setzen von Bohrhaken mit Spreizdübel ist darauf zu achten, dass beim Einschlagen des Dübels kein Metallhammer verwendet wird (weil sonst Kerben entstehen können), dass das Drehmoment beim Anziehen der Schraubenmutter beachtet wird und dass keine verschiedenen Stahlqualitäten gemischt werden.
Mehr: